Delving Deeper into the Complexities of Sodium Alginate and Other Alginates Manufacturing
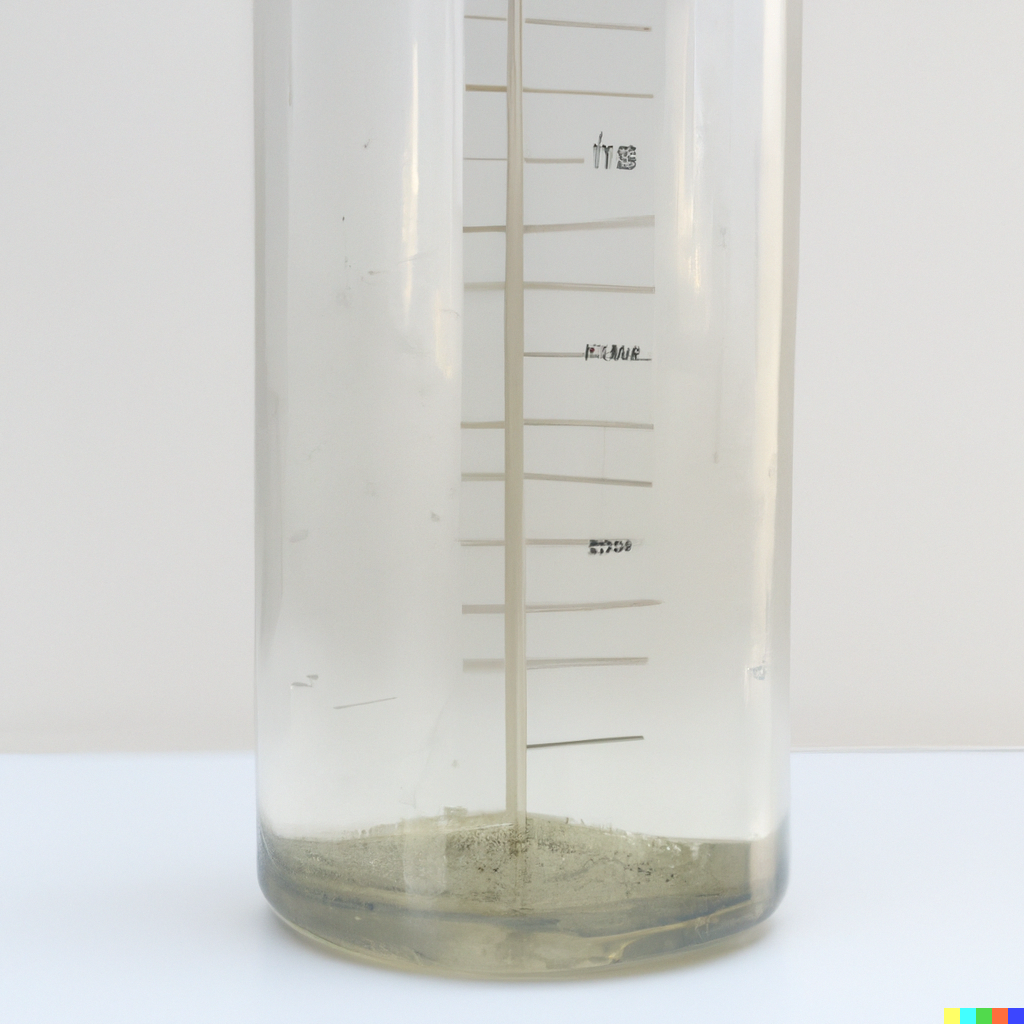
Sodium alginate, a polysaccharide derivative derived from brown seaweed, has found applications in various industries ranging from food and textiles to pharmaceuticals and biotechnology. Despite its wide range of applications, the production of sodium alginate and other alginates presents unique challenges that require a profound understanding of the chemical and physical properties of these polysaccharides. Among these challenges, issues of stability, phase separation, syneresis, and the equilibrium among different cations have been a particular concern. This article elucidates these complexities and presents the strategic solutions implemented to overcome these challenges.
Chemical Equilibrium Among Different Cations
Sodium alginate, like other polysaccharides, has a polymeric structure consisting of mannuronic acid (M) and guluronic acid (G) residues. The arrangement and distribution of these residues have significant implications for the interactions of alginate with different cations, thereby influencing the behavior of alginate in solution. One of the critical aspects investigated during this project was the chemical equilibrium among different cationic species, namely sodium, calcium, and magnesium ions.
In solution, sodium alginate tends to exchange its sodium ions with divalent cations like calcium and magnesium, leading to a shift in the chemical equilibrium. This can potentially cause gelation or precipitation, given that calcium and magnesium ions form stronger links with the G-blocks of alginate, thereby disturbing the stability of the solution. By controlling the ratio of these cations in the process environment, their impact on the alginate solution's stability could be significantly mitigated.
Appearance of 'Threads' in Sodium Alginate Solutions
A particularly intriguing phenomenon observed during the project was the appearance of 'threads' or 'strings' in the sodium alginate solution. These 'threads' can be attributed to the hydrodynamic and thermodynamic characteristics of sodium alginate in solution. The long-chain polymers can interlink and form networks that manifest as thread-like structures when the solution is drawn out or disturbed.
These threads may pose issues during manufacturing, particularly in operations requiring uniform solutions or in processes where these threads may entangle with machinery. Thus, understanding the formation of these threads and controlling their occurrence through factors such as solution viscosity, temperature, and stirring speed became an essential part of the project.
Efficient Mixing, Stirring, and Energy Transfer in Emulsions
The project also focused on the dynamics of mixing and stirring and how these processes influence the stability and quality of alginate solutions. Efficient mixing is critical to form homogeneous solutions and emulsions, particularly in the case of alginates that are often used as emulsifiers and stabilizers.
The stirring process imparts kinetic energy to the solution, facilitating the break-up of larger alginate particles into smaller ones. The energy transfer during stirring promotes the dispersion of the alginate throughout the solution, thereby forming more stable emulsions with smaller droplet sizes. This is based on the principle that smaller droplets have a higher surface area to volume ratio, which can lead to a lower overall surface energy and thus a more stable emulsion.
However, the energy input must be carefully controlled, as excessive energy can lead to shear degradation of the polysaccharide chains. Thus, the stirring process should be optimized to achieve a balance between efficient mixing and preserving the integrity of the alginate chains.
In-Depth Solutions
Throughout the project, several solutions were implemented to address these complexities. The pH range was carefully controlled to maintain optimal alginate stability. The use of softened or treated water helped mitigate the impact of hard water components like calcium and magnesium ions. The quality of DI water was strictly monitored to ensure the absence of any impurities or microbial contaminants that might destabilize the alginate solution. The addition of polymeric stabilizers such as xanthan gum, locust bean gum, and guar gum helped prevent phase separation and syneresis by forming a protective gel network around the alginate particles.
Moreover, the appearance of 'threads' in the alginate solution was controlled by adjusting solution viscosity, temperature, and stirring speed. The stirring process was optimized to provide efficient mixing and energy transfer, enabling the formation of smaller, more stable alginate particles in the emulsion.
The Concluding Act
The challenges encountered in this project underscored the intricacies of sodium alginate and other alginates manufacturing. The experiences gleaned from the project reinforced the necessity of a scientific and systematic approach to problem-solving. The implemented solutions – pH control, water quality management, use of polymeric stabilizers, control of thread formation, and optimized mixing and stirring – all contributed to significant improvements in the stability and quality of the alginate products.
This intricate exploration of alginate manufacturing is an attestation to the fact that science and industry are deeply intertwined, each shaping and influencing the other. In conclusion, the complex journey of navigating and resolving the challenges associated with sodium alginate manufacturing serves as a testament to the evolving and exciting field of polysaccharide science and industry.