E10 gasoline additives investigation
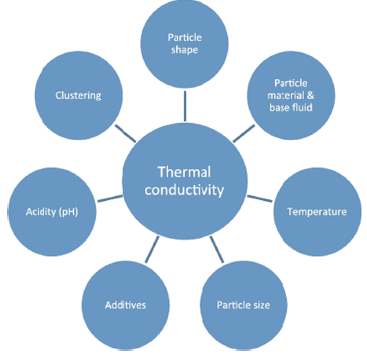
The main issue for this work was to investigate:
n Whether the current E10 additives are sufficient to mitigate/ eradicate reported problems due to the ethanol content
n Identify weak spots in machines, especially older ones, due to the ethanol content
n Identify potential solutions to any of these issues so that the organization could manufacture some of their own, or even directly use some of their existing chemicals for these purposes
The main issues that arise due to the ethanol presence are due to the hygroscopic nature of ethanol that can attract and retain water, and thus promote corrosion of parts. This problem has been well addressed and managed via the use of corrosion inhibitors and pH buffers to protect such susceptible components. The weak spot that admittedly remains is that of some system seals. Another issue that has been widely discussed, is that of elastomer compatibility. A number of published works addresses this issue that could cause swelling, shrinking and cracking of elastomers, mostly seals and flexible pipes and other unsuitable gasket materials. A third reported cause of concern is a potential air/ fuel ratio modification. Additives that contain potassium, phosphorous, manganese and sodium are common additives of aftermarket additives that are currently used for older vehicles, although some restrictions exist when it comes to newer ones.
The main materials that seem to be susceptible to structural, physical and chemical damages include cork, shellac, epoxy resins, nylon, polyurethane and some glass fiber reinforced polyesters. All of these materials are known to be affected by ethanol presence. Physically, one can understand the effect if two parameters are taken into consideration:
1- The small size of ethanol in comparison to the hydrocarbons in gasoline, allows it to diffuse into the pores of the mentioned components
2- The lower affinity (cohesion) of some material molecules in comparison to their affinity to ethanol allows the ethanol molecules to enter the cavities in their structures and swell them. When a drying cycle occurs, and depending on the conditions of the cycle, removal of ethanol could lead to cracking and opening of those materials. Still, this depends on the chemical and physical environment around those components.
Our work focused on:
- Finding materials that were more ‘compatible’ with ethanol
- Identifying suitable protective coatings for the components of interest
- Identifying novel mixtures with E10 additives that can mitigate the issue
Our work has led to the quest of new formulations, especially some based on natural anti- oxidants, but also some synthetic ones