CMAS molten deposits on Thermal Barrier Coatings: Novel solutions
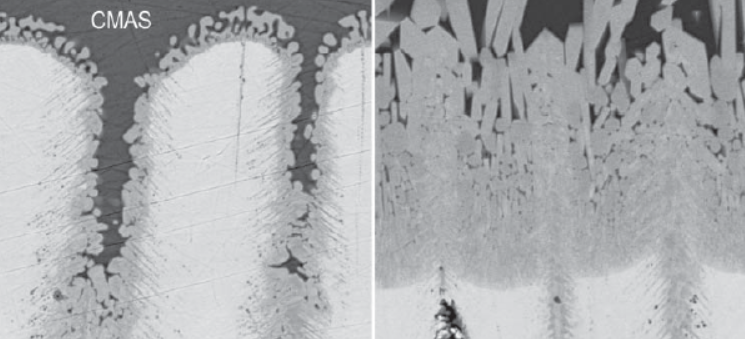
Perhaps the greatest issue nowadays for Thermal Barrier Coatings self life and efficiency comes from the deposit of molten Calcium Magnesium Alumino Silicates (also termed as CMAS). These deposits come mainly from atmospheric debris and they melt on the thermal barrier coating surfaces or during their travel towards the TBC surface. These deposits can cause the dissolution of thermal barrier coatings into them, opening cracks down to the metal surface and causing complete destruction of both TBC’s and composite’s integrity. The problem is of even higher significance in the case of high temperature gas turbines (1400-1500K currently) where the molten deposits lead to deactivation of thermal barrier coating protection.
Different approaches have been suggested by academia and industry for the minimization of molten CMAS deposits effects. In general, for a solution to be effective, the following have to be addressed:
· Thermal barrier dissolution kinetics need to be slowed down or totally come to a stop
· Dissolution and mineralization are also competitive processes and the second could be used against the first
· Multiple resistances could be used to slow down penetration of molten CMAS deposits towards the composite surface
Molten CMAS deposits initiate the degradation procedure by diffusing through the thermal barrier coating’s pores and in their path they cause the instant dissolution of TBC. Upon dissolution re- crystallization occurs with unstable phases creation and precipitation that both increase thermal conductivity and minimize porosity and mechanical properties of the whole thermal barrier coating.
One recent work has dealt with different solutions, including:
- The use of a Samarium Zirconate coating (SZO) on top of a classical Yttria Stabilized Zirconia (7%).
- The use of an additional platinum coating as an external film for Samarium Zirconate
The experimental investigation lead to the findings that the Samarium Zirconate coating significantly increased the resistance of thermal barrier coating from 1 minute to 4 hours for complete penetration. This finding suggests that Samarium Zirconate alone could be a feasible solution for high temperatures and short time exposures to thermal shock. However, the additional placement of the platinum layer on top of the Samarium Zirconate lead to an amazing increase of chemical resistance with 16 hours of exposure with no complete penetration of thermal barrier coating. This result is one of the most prominent ever published. The CMAS used in this work was a 33CaO – 9MgO – 13 AlO1.5 – 45 SiO2 at 1250 °C.
Another very effective approach includes the use of various contents of Al2O3 and TiO2 as a solid content of Yttria stabilized Zirconia. Long investigations have revealed that the use of a 20% Al2O3 and 5% TiO2 into YSZ led to excellent mitigation of the molten CMAS effects on thermal barrier coatings. Solution precursor plasma spray (SPPS) process can be used as the manufacturing approach for these tailored thermal barrier coating structures. The mechanism of this approach is dual; Al and Ti serve different functions. Initially Al promotes very easy crystallization in the molten glass phase. Ti then serves as a nucleating agent for the modified melt and the fast crystallization blocks the available porosity and thus stops the penetration process of the molten CMAS towards the composite surface. The crystallized structure is anorthite that effectively stops any further diffusion.
Another known solution is the use of Gadolinia based TBCs. Recent works have shown that Gadolinia based solutions have hindered penetration of molten CMAS deposits and further degradation of both thermal barrier coating and underlying composite. Gd Zirconate is currently a very popular approach for CMAS deposits resistance. Other rare earth zirconates are also under investigation based on Gd zirconates results.
Melting, re-crystallization and diffusion hindering can very accurately be examined with the proper atomistic simulation and CFD simulation approaches. In the case of atomistic simulation, the local crystallization pathway can be monitored at real time while CFD simulation allows for the investigation of porosity blocking, diffusion hindering and reaction rate minimization. Combination of the atomistic simulation and CFD simulation allows for a complete prediction of the thermal barrier coating protection procedure. Our experts at SinodosChemistry.com will guide you through the process of predicting the thermal barrier coating deterioration process.