Introduction to thermal fluids
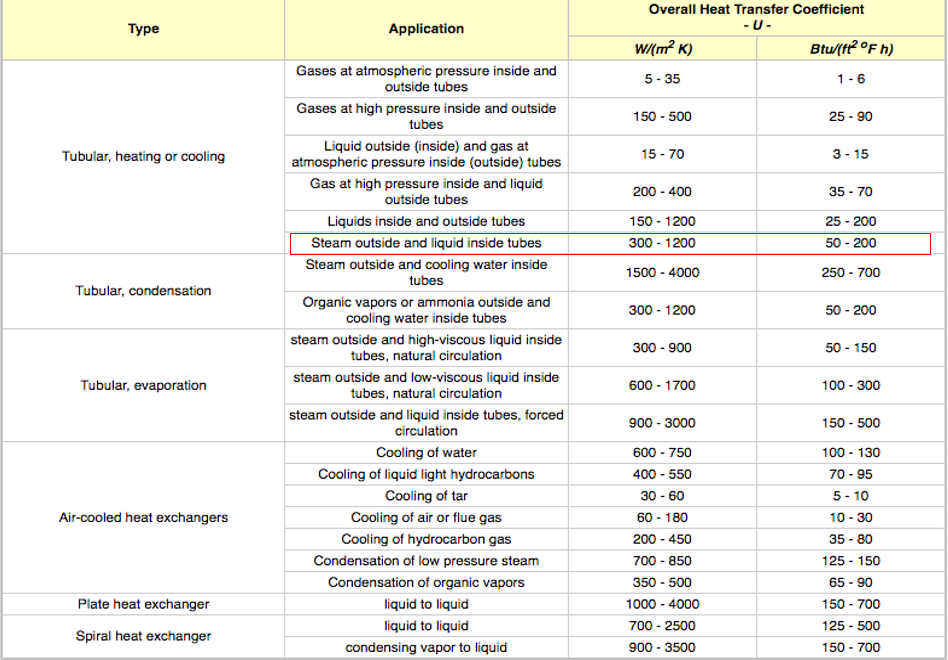
Heat transfer is a major component of chemical, manufacturing and industrial processes. Thermal exchange systems can be direct or indirect (with the employment of thermal fluids). Direct heating technology involves direct contact between materials to change the final temperature. On the other hand, indirect heating technology does not allow the product to come in contact with the heating agent (thermal fluid) to change the final temperature. Indirect heat transfer uses conduction, radiation or convection to achieve temperature change.
There are several types of technologies used for direct and indirect heating of fluids or solids. However, for the heat exchange procedure to be carried out correctly it is necessary to select an appropriate fluid as heating agent. In other words, the specification of which thermal fluid will be used is indubitably one of the most important specifications to set when designing a heat transfer system and is able to maximize efficiency and decrease costs. Heat transfer fluids are used because they require low maintenance and generally have low corrosion, environmental safety and precise temperature controls. The main applied thermal fluids are:
Water: Presents as advantages the low cost and environment preservation, it is not toxic or flammable, it has good thermal stability and high heat transfer coefficient. However, the boiling point is lower compared to the other options and therefore isn’t suitable for all applications.
Glycol: Normally used for process cooling, however it is very efficient for heating due to the high specific heat capacity, high thermal conductivity and low viscosity. Glycol thermal fluids can operate at higher temperatures than water, however are more expensive.
Glycol/water mixtures: Result in a thermal fluid with higher boiling point and lower freezing point comparing to the pure fluids. However, despite the advantage, the mixture presents some reduction in heat capacity.
Thermal oils: Present higher boiling points which can be reached without increasing overly the pressure of the system and are chemically stable at high operating temperatures. Some synthetic thermal oils can make the system reach 800 °F. Thermal oils are also typically non-corrosive and don’t need to be treated, as water, to prevent hard water deposits from forming in the system. The thermal oils can be classified in mineral and white oils (petroleum-based fluids), synthetic fluids, which are modified benzene compounds, and silicon and fluorocarbon-based fluids, considered as specialty fluids, presenting higher costs compared with the organic and mineral ones.
It is quite common to face industrial processes requiring temperatures that easily exceed 300 or 400 ºC and, in these cases, the use of water to perform the heat exchanges can imply in serious risks due to the high pressure generated by the steam. The thermal fluids require lower pressures, mainly to be pumped over the system, are less reactive and less corrosive than water, and present excellent thermal stability in the operating temperature range. In this case it is possible to have a more controlled and safer process.
The thermal fluids are also very important for refrigeration applications, for example, to remove heat from reactors. In this case, as the fluid circulates, heat transfer cools the system, and the fluid can dissipate heat elsewhere. To prevent heat waste, the system can use the it to produce energy or to supply temperature to another zone in the process.
Since there are numerous thermal fluids available and with specific heating and cooling properties ideal for a wide range of industrial processes, some knowledge is required in order to make the right choice of this product. The choice of the thermal fluid must be related to the efficiency of the system, considering requirements such as:
Thermal stability: Related to the capability of a heat transfer fluid to withstand the molecular cracking due to the thermal stress. In this way, the thermal stability is fundamental to determine the maximum operating temperature of a fluid.
Maximum process temperature à Maximum temperature to which the fluid can be exposed without starting the degradation process. Most fluids will begin to deteriorate at an accelerated rate when exposed to temperatures above this.
Maximum fluid temperature à It refers to the temperature that the fluid film reaches inside the heater when in direct contact with the heat transfer surface. The film temperature rating is generally about 50 °F (27.7 °C) above the maximum mass temperature.
Viscosity: It is of great importance to understand and interpret changes in viscosity. Most heat transfer fluids exhibit large changes in viscosity between ambient and operating temperatures. Fluids that exhibit high viscosity at lower temperatures can be problematic in cold startup conditions. It is of great importance to understand changes in viscosity. Most heat transfer fluids exhibit large changes in viscosity between ambient and operating temperatures. Fluids that exhibit high viscosity at lower temperatures can be problematic in cold startup conditions.
Vapor pressure: The increment in temperature causes an increase in the vapor pressure of the fluid. In this way, the vapor pressure is very important to know when specifying and designing the pumps.
Density: This property is also used for correctly sizing the circulation pump and also for determining the size of the expansion tank.
Specific heat: Measure relative to the thermal variation of the fluid when receiving a certain amount of heat, that is, the amount of heat necessary for each gram of a substance to undergo a temperature variation corresponding to 1 °C. Assists in determining the fluid flow rate needed to achieve desired process conditions.
Heat transfer coefficient: Value used for calculating the heat transfer. It is referred to how efficiently heat is conducted through a variety of resistant media.
In addition, other characteristics are also important when making decisions regarding the thermal fluid, such as possibility of attack to the system's construction material, toxicity and irritability to the skin or mucous membranes, presence of strong odors, costs and facility in obtaining.
Finally, after all the considerations, choosing the appropriate fluid should initiate with the selection on the type of heat transfer fluid best fits the general scenario within the possibilities. Then, comparisons between individual fluids in the same group will probably drive to solution of the specific goal.