Petrochemicals outlook [May 2016]
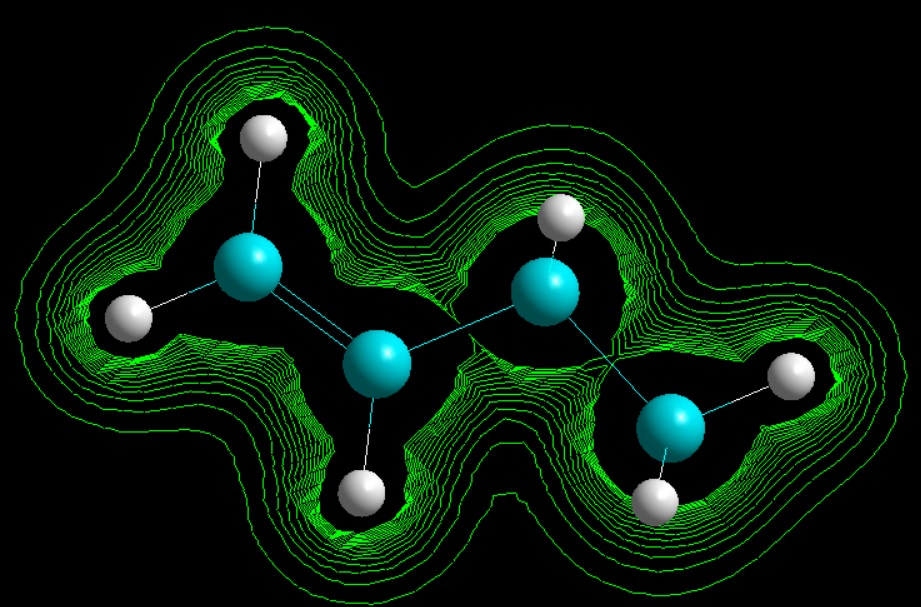
Petrochemical is a vast category of chemicals derived from oil and gas. They can be described by categorization of the most important of them into base chemicals, intermediates, formulated products and end – uses. Most important base products include:
- Olefins [ethylene, propylene, butylene]
- Aromatics [benzene, toluene, aromatic amines, xylenes, etc]
- Alcohols
- Carboxylic acids
- Amines
- Alkanes
Most important formulated products derived by these basic chemicals are:
- Plastics and resins [such as extruded films, coatings, sheets, and foams]
- Synthetic fibers
- Rubbers
- Adhesives and sealants
- Lubricants
- Paints
- Coatings
- Cleaning agents
- Industrial chemicals
- Flame retardants
And many other secondary categories. These formulated products are used in a range of activities and applications covering:
- Automotive
- Consumer products
- Transportation
- Packaging
- Construction
- Industrial
- Pharmaceuticals
- Medical
- Textiles
- Electronics
- Aerospace
And other secondary categories.
Petrochemicals market in 2014 was evaluated at around 550B$. Most predictions suggest that the market will reach 880-900B$ by 2020. This trend is mainly supported by an increasing demand for Ethylene and Methanol which accounted for one quarter of the total petrochemical market in 2014. Polypropylene demand [PP] and propylene oxide are the main two products exhibiting the increased demand. PP’s main uses include textiles, packaging, stationery applications, automotive and others. Methanol on the other hand is used as a solvent in a number of chemical transformations, as gasoline additive, as the first material for the manufacturing of olefins, and other uses.
Benzene is another popular organic solvent that despite its health and environmental effects [it has proven to be carcinogenic and contributes to VOC emissions and pollution is expected to grow steadily up to 2020, reaching a record high of 42 M tons. Benzene is also used in a series of transformations and is the first raw compound in a series of organic families like aromatic amines, aromatic acids, and others.
The largest market in petrochemical consumption is Asia [estimated 50% of total consumption] with China being the undisputed leader. A major transformation that is expected to continue in the years to come is the total shift of manufactures from US and Europe to Middle East countries and especially Saudi Arabia and UAE. Those regions provide operational advantages that include abundance of first materials and know-how that has been acquired during the last decades. New manufacturing methodologies and new research and development centers in Saudi Arabia have attracted world class specialists in the region.
During the beginning of 2016, US initiated ethane exports to Europe. Iran has announced that they are going to double their PE manufacturing up to 8 M tons by 2022. Recently Aramco and Total have announced that they decided on a 10% expansion in the capacity of their joint refinery in Saudi Arabia. Royal Dutch Shell have announced that their US based project was ‘on hold’ possibly due to thoughts about activation in Middle East.
Petrochemical industry is greatly dependent on the additives industry for the production of polymers and composites. In short, the most important additives for polymer industry are presented in Table 1:
Table 1: Additives in the polymers industry
Function | Additives |
Fillers & Re enforcing agents: Inorganics |
Oxides [MgO, SiO2] Hydroxides [Al(OH)3] Metals [Boron, Steel fibers] Silicates [Talc, Mica] |
Fillers & Re enforcing agents: Organics |
Carbon Carbon black Graphite Aramic fibers Cellulose fibers PET PE PVA |
Plasticizers |
Trialkyl phosphates Adipates Chlorinated paraffins Polyesters Epoxy derivatives Phthalate esters |
Impact modifiers |
EPDM NBR NR EVA MBS CPE Elastomers |
Cross linking agents |
Organic peroxides Rubber curatives |
Flame retardants and smoke suppressants |
Sb2O3 Chlorinated paraffins Al(OH)3 Mg(OH)2 Organophosphate esters Zinc borate Brominated organic compounds Molybdate salts |
Conductive agents |
Carbon black Graphite fibers Metals Metallized fibers |
Processing additive: stabilizers |
Primary antioxidants Hydroperoxide decomposers Acid adsorbers |
Processing additive: lubricants |
High molecular weight fatty acids High molecular weight fatty acids derivatives Paraffin waxes Metal soaps Ester and amide waxes Silicones Polyfluoro carbons |
Processing additive: flow and fusion promoters |
PMMA MBS Acrylic ester copolymers |
Processing additive: Thixotropic agents |
Fumed silica Clays |
Antiaging: Antioxidants |
Sterically hindered phenols Sec- aromatic amines Phosphates Thioethers |
Antiaging: metal deactivators |
Chelating agents |
Antiaging: Light stabilizers |
Pigments UV absorbers [hydroxyphenones] Excited state quenchers [Organic – Ni complexes] Free radical scavengers Hindered amine light stabilizers |
Antiaging: Biostabilizers |
Copper quinolinolate Phthalimides Thio compounds |
Surface modifiers: antistats |
Ethoxylated amines Phosphate esters Glycerides |
Surface modifiers: antifoggers |
Fatty chain glycol surfactant Polyether surfactants |
Surface modifiers: antiblocking and slip additives |
Silica Amide waxes Oleamide |
Surface modifiers: antiwear |
Graphite MoS2 PTFE |
Surface modifiers: wetting agents |
Ionic surfactants Non ionic surfactants |
Surface modifiers: adhesion promoters |
Silanes Titanates Block and graft copolymers |
Pigments |
Ti, Fe, Cr oxides Cd, Ba, Pb sulfides, chromates and sulfates Carbon black Phthalocyanines Quinacridones Azo pigments SiO2, talc, sodium benzoate Anthraquinones Azo and bisazo compounds |
Blowing agents |
Hydrocarbons, halocarbons CO2, N2 Bicarbonates Benzene sulfonylhydrazides Tetrazoles |
Depending on type of polymer required, various forming processes are used, including:
- Sand casting
- Dye casting
- Investment casting
- Low pressure casting
- Forging
- Extrusion
- Sheet forming
- Powder methods
- Electro machining
- Conventional machining
- Injection molding
- Blow molding
- Compression molding
- Rotational molding
- Thermo forming
- Polymer casting
- Resin transfer molding
- Filament winding
- Lay up methods
- Vacuum bag